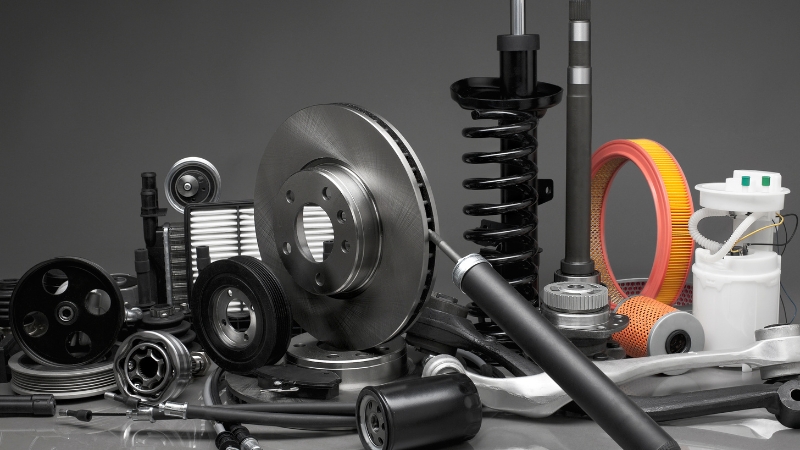
Share Post:
Electric vehicles are everywhere in 2025, gaining popularity across all segments, from luxury sedans to compact commuters.
As more drivers shift to electric power, questions about long-term ownership costs surface quickly.
One area that continues to raise eyebrows is the replacement cost of EV components.
Unlike internal combustion engine (ICE) vehicles, where part replacement is often more straightforward and cheaper, EVs introduce high-tech components and complex systems that come with steep price tags.
1. High-Voltage Battery Pack
High-voltage battery packs define an electric vehicle’s performance, range, and long-term usability. Each pack contains hundreds to thousands of lithium-ion cells grouped into modules, surrounded by cooling loops, impact protection structures, and control electronics.
All components are managed by an onboard Battery Management System (BMS), which coordinates charge distribution, thermal stability, and safety protocols.
Manufacturing these packs involves costly raw materials. Lithium, nickel, cobalt, and graphite must meet strict purity levels and undergo extensive processing. Supply chain volatility for these elements drives pricing upward.
In addition, battery packs are model-specific and non-interchangeable. Engineers design them to fit precisely within a vehicleโs chassis, often integrated into the floor structure, which raises manufacturing and repair costs.
Temperature regulation is handled by active liquid or refrigerant-based cooling systems. Any leak or sensor failure in the thermal control network adds to the labor burden.
Examples:
- Tesla Model S: Up to $22,000 for replacement
- Hyundai Ioniq 5: Reported estimates from $6,300 to $36,000
- BMW i3: Dealer quotes reaching $71,000
Without warranty coverage, battery replacement can equal or exceed the vehicleโs resale value.
Once factory coverage ends, extended protection plans or specialized vehicle policies become essential.
Options like NRMA Insurance can cover key components such as the battery pack, charging hardware, or even infotainment systems.
2. Electric Motor
Electric motors are often highlighted for smooth performance and minimal maintenance needs. Despite this, failures, though infrequent, can lead to high repair bills.
Most electric motors in EVs are not designed for easy disassembly or part-level repair, meaning full replacement becomes the default solution.
Precision engineering plays a central role in their performance. High torque delivery, instant acceleration, and quiet operation rely on a combination of advanced materials, magnetic systems, and cooling mechanisms.
A few reasons make electric motors expensive to replace:
- High-quality rare-earth magnets are used for optimal torque density
- Advanced copper windings are designed to handle rapid acceleration and deceleration cycles
- Integrated cooling and control systems that regulate heat and ensure thermal stability
- Compact, dense packaging that allows for efficient space use within the vehicle chassis
Rebuilding is rarely an option due to proprietary designs, sealed casings, and high-voltage risks. Even diagnosing the issue can take hours using manufacturer-specific diagnostic tools. Replacement becomes the only safe and viable option in many cases.
3. Charging System (Onboard Charger & Ports)
Charging systems in electric vehicles include several integral components that handle both power delivery and safety.
These include the onboard charger, responsible for converting alternating current (AC) into direct current (DC), external charge ports for physical connection to the grid, and signal-handling units that regulate voltage and communication protocols.
Failures in this setup are not rare, especially as vehicles age or encounter unpredictable power conditions.
Problems often begin with heat buildup inside the charger housing during long charging sessions. Consistent exposure to elevated temperatures reduces efficiency and accelerates the degradation of internal circuitry.
Voltage spikes during rapid charging sessions can short internal components or damage the power conversion system. Additionally, repeated fast-charging sessions put additional strain on the system and may trigger premature failure.
Port damage is another concern and often stems from physical abuse or environmental wear. Insulation around connectors may degrade due to moisture, temperature swings, or basic wear and tear. Improper alignment or forcing the plug into place can bend contacts or stress the surrounding wiring.
Several failure-prone situations include:
- Onboard charger burnout due to thermal overload or internal arcing
- Port wear or breakage caused by excessive force or incorrect handling
- Water intrusion in the charge port seals during seasonal exposure
- Firmware mismatch between new charging units and vehicle software
4. Inverter/Converter Systems
Inverter and converter systems serve as critical electrical mediators in EVs. Inverters transform the DC current stored in the battery into AC current required by the motor.
Converters manage bidirectional power flow, especially during regenerative braking, converting kinetic energy into usable battery charge.
These units handle continuous power switching at high voltages and must perform with speed and precision.
High loads, repeated thermal cycling, and voltage fluctuations gradually wear out internal components. Even minor damage, such as heat stress or microfractures in the power electronics, can result in catastrophic failure.
Unlike some other systems, inverter/converter units typically offer few serviceable parts. Once diagnosed as faulty, the entire component is often replaced rather than repaired.
Key points to consider include:
- High wear environments: Constant voltage transitions and heat cycles.
- Overheating, short circuits, electrical noise issues.
- Most systems are sealed and proprietary.
- Shops may charge $300โ$600 just to confirm failure.
5. Battery Management System (BMS)
View this post on Instagram
A post shared by CS Electrical and Electronics (@electrical_and_electronics_cs)
Battery packs do not function optimally without a tightly controlled environment. That task belongs to the BMS.
This system is responsible for real-time monitoring and control of battery health. It regulates voltage, current, and temperature across hundreds of individual cells.
Failure in the BMS may not immediately trigger a warning. Drivers may first notice range dropping faster than expected, battery overheating during charging, or inaccurate state-of-charge readings.
Diagnosing BMS failure is complex. Software tools needed for accurate assessment are typically available only to manufacturer-certified technicians.
Key symptoms and considerations include:
- Unexplained range drops, false dashboard errors, temperature spikes.
- System may appear operational, but operate with degraded safety margins.
- Often requires battery removal for inspection.
- Limited to authorized service centers.
6. HVAC Heat Pump Systems
@evhacs Why put EV Chargers into heat pumps or air conditioners? #electricvehicles #EV #evchargers #evcharging #evcharginginfrastructure #evchargingstations #evchargingsolution #heatpump #hvac #hvacsystem #irishbusiness #newtech #newtechnology #loadbalancing #sustainability #sustainableliving #sustainabletech #sustainabletechnology โฌ original sound – evhacs
Heat pump systems in EVs replace traditional resistive heaters. These systems operate more efficiently, drawing less energy from the battery.
Tesla Model Y, for instance, relies heavily on its heat pump for cabin climate control and battery preconditioning. A malfunction can impact driving range and user comfort.
Repairing or replacing heat pumps involves disassembling the HVAC housing, recalibrating the climate system, and verifying software compatibility.
Winter driving without it becomes a frustrating experience.
7. Infotainment and Digital Instrument Clusters
Infotainment systems in EVs have moved far past simple radio or CD functionality.
Central touchscreens now manage core operations like drive mode selection, battery range visualization, climate control, navigation, and even activation of safety systems such as lane assist or collision avoidance.
When one of these screens fails, it doesnโt just affect entertainment; it impacts daily drivability.
Failures can cascade across multiple subsystems. For example, a touchscreen malfunction may also disable access to HVAC controls or driving modes.
Replacement is rarely straightforward, since compatibility must align with the vehicleโs firmware, and software reprogramming is often mandatory during installation.
Owners should be aware of the following key points:
- Touchscreens are mission-critical components, not cosmetic features.
- Digitizer faults or minor cracks may require replacing the entire unit.
- Firmware compatibility issues can delay or complicate replacements.
- Replacements usually require software reprogramming by certified technicians.
- Aftermarket parts often fail due to proprietary software locks.
8. Regenerative Braking System Components
Regenerative Braking System Electric Vehicles, its Component and Working Systemhttps://t.co/XmH0hurUno#electricvehicles #electriccars #electricscooters #batteries #regenerativebraking #ev #technolocy
โ Electric Vehicle Info (@evehicleinfo) September 7, 2024
Regenerative braking captures kinetic energy during deceleration and routes it back into the battery, boosting efficiency and extending range.
The system includes sensors, control units, software, and brake actuators, all of which must work in precise harmony.
Component wear, faulty actuators, or mismatched software updates may lead to reduced regeneration or ineffective braking altogether.
Since braking feedback is often blended with traditional hydraulic brakes, inconsistencies can confuse the driver and diminish confidence.
Important technical aspects include:
- Electronic control modules are responsible for energy conversion logic
- Brake actuators that apply variable resistance based on vehicle speed
- Software calibration maps linking regeneration strength to pedal input
- Sensor networks that monitor wheel speed, torque, and battery charge
Replacing a failed part may require recalibrating control modules and reprogramming software.
Even after parts are swapped, calibration is essential to restore brake feel. If skipped, drivers may experience jerky braking or unexpected stops.
Summary
Electric vehicle ownership brings many benefits, but high replacement costs for key components remain a serious consideration.
Factory warranties for major systems, especially batteries, often cover 8 years or more. After that period, extended protection plans and certified repair centers become essential for peace of mind.
Battery cost per kWh is dropping steadily, offering hope for more affordable replacements in the future. Until those savings fully reach the aftermarket, EV owners need to plan carefully and budget wisely.
Related Posts:
- Inside the Rolls-Royce La Rose Noire Droptail -…
- Easiest Way to Replace Cabin Air Filters in Under 10 Minutes
- TRQ Auto Parts - The Truth About Their Quality & Reliability
- The Most Reliable Used Electric Cars to Buy in 2025
- 5 Most Exciting Spec Racing Cars You Need to See in 2025
- Which States Have the Most Car Accidents in 2025?…