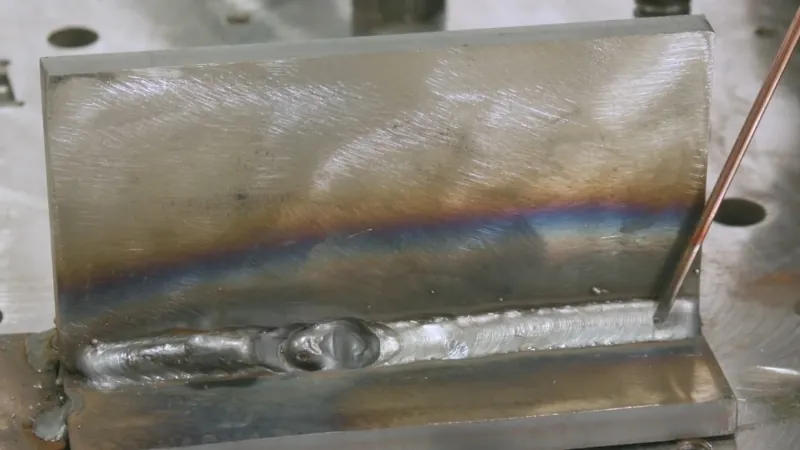
Share Post:
Welding might look like sparks and fire to the untrained eye, but anyone whoโs worked with frames, whether on a vehicle chassis, structural machine housing, or aerospace skeleton, knows itโs all about precision.
A little too much heat here, the wrong arc settings there, and over time, the frame that once looked solid and clean can start to sag, crack, or just… soften.
At the heart of this problem lies one of the most misunderstood aspects of modern MIG welding: pulse settings. When configured right, pulse MIG is a gift. It gives you cleaner welds, less spatter, and better control, especially on materials like aluminum or stainless.
But if the settings are even slightly off, the long-term consequences can be severe, especially when it comes to frame softening.
Letโs walk through whatโs really happening under the hood and how to keep your welds tight, strong, and built to last.
Table of Contents
ToggleWhat Is MIG Pulse Welding and Why It Matters for Frames
MIG pulse welding, or GMAW-P, isnโt your basic wire-feed MIG setup. It alternates between a high peak current and a lower background current, cycling rapidly, anywhere from 0.5 Hz to over 500 Hz on industrial machines.
That alternating rhythm does more than just sound fancy:
- It controls heat input, helping avoid burn-through and distortion.
- It improves bead appearance and reduces post-weld cleanup.
- It makes welding high-strength or heat-sensitive materials more manageable.
That last part is why itโs often used for structural frames. Frames made from materials like 6061-T6 aluminum or high-strength steel donโt play well with excess heat.
So, welders lean on pulse MIG to stay within safe temperature zones while getting strong, reliable welds.
But if you mismanage the pulse settings, you donโt get those benefits. You get heat. Too much of it. And thatโs where the trouble starts.
Pulse MIG is powerful, especially for frames, so if you suspect any distortion, bring it to a certified auto repair shop.
The Heat Factor & Why Frames Are So Sensitive
Letโs talk about heat input for a second. Welding always involves heat, but when it comes to frames, the key is not just how much heat you add, but how fast, where, and for how long. In pulse MIG, several dials control this:
- Peak Current โ delivers the punch to push metal droplets across the arc.
- Background Current โ keeps the arc alive between pulses.
- Pulse Frequency โ determines how often current flips between high and low.
- Pulse Balance โ controls how much time is spent in each current phase.
- Travel Speed โ slower travel means more heat per inch of weld.
Now apply that to frame welding. Frames have to take repeated loads, vibrations, and, especially in vehicles, road abuse. When you overcook the material with poor settings, you alter the metal around the weld, also known as the Heat Affected Zone (HAZ).
In aluminum, for example, this heat can dissolve or coarsen tiny strengthening particles like MgโSi. Once that happens, the surrounding area becomes soft, and weโre not talking about a little softness.
In 6061-T6, strength loss in the HAZ can hit 30 to 40 percent. Thatโs like welding a high-strength frame and ending up with a soft aluminum soda can on the sides.
Real-World Frame Softening Triggers
Hereโs where a lot of welders get into trouble. You set your machine based on experience, or you go with a chart on the side of the welder and figure โclose enough.โ
But with MIG pulse, especially on aluminum or thinner gauge steel, small mistakes can snowball fast.
1. Cranking Peak Current Too High
Say you’re working with 1/8″ aluminum and dial your peak current to 250 amps. Sure, youโll get great penetration. But youโll also put way too much heat into the area, especially if your travel speed isnโt fast enough to keep things moving.
2. Background Current Not Low Enough
Background current should chill things out between pulses. If itโs sitting too high, say at 70% of your peak, itโs not really giving the material a break. Youโre running hot constantly, even when you think youโre โresting.โ
3. Low Pulse Frequency
At 60 Hz or lower, your pulses are stretched out. That gives each high-current period more time to heat up the workpiece. On thin frames, you want more frequent, shorter bursts, usually 100 Hz or more, to keep temps in check.
4. Unbalanced Pulse Timing
A 70/30 split in favor of peak current sounds good if youโre trying to burn into thick steel. But on an aluminum bike frame or truck subframe, itโs a recipe for structural soft spots. A more neutral or background-heavy balance keeps the average heat lower.
What Long-Term Frame Softening Looks Like
Itโs not always obvious right away. A freshly welded frame looks perfect on the surface. But give it a year or two, a few thousand miles, a season of machinery use, and things start showing up:
- Creep: Sections start bending slightly under constant loads.
- Cracks: Fatigue cracks appear, especially near weld toes.
- Sagging: Misalignment grows over time due to soft zones losing stiffness.
- Unexpected Breaks: Welds that looked good on day one just give out.
One mechanic shared a case where a truck chassis repair was done with a pulse MIG setup using stock settings.
Two years in, the frame had sagged so much that wheel alignment couldnโt be maintained. The weld hadnโt failed, but the surrounding HAZ had lost its strength.
Common Mistakes That Lead to Overheating
Mistake
Consequence
Peak Current Too High
Deep HAZ softening, burn-through
Background Current Too High
Cumulative overheating, wide HAZ
Low Pulse Frequency
Slower transitions, more time at peak heat
Incorrect Pulse Balance
Overexposure to peak current
Travel Speed Too Slow
Increased heat input per inch
Inadequate Gas Flow
Porosity, poor arc stability
Wrong Shielding Gas
Excess oxidation, inconsistent arc behavior
Aluminum vs. Steel Frames
Aluminum (e.g., 6061-T6)
- Most sensitive to overheating
- Strength comes from precipitation hardening
- Once precipitates dissolve or coarsen, strength drops fast
- Often requires re-aging after welding
High-Strength Steel
- Better at tolerating heat, but still prone to distortion and softening
- Pulse MIG helps avoid over-penetration on thinner parts
- More forgiving with post-weld strength, but harder to reshape once softened
How to Prevent Frame Softening
@welddotcomIf you are trying to MIG weld aluminum you have a few options. First you can get away with running it around 10 feet using a teflon liner. Another option is using a spool gun or if you want to big rolls of wire use a push pull gun like this Freedom Drive from Abicor Binzel, which will help keep the wire tight through the MIG gun over long distances because of the drive rollers pulling the wire as well as the machine pushing the wire. Watch the full video showing different ways Not to MIG weld aluminum on YouTube https://foxly.link/Iv6p90 #mig #migwelding #aluminum #spoolgun #pushpull #abicorbinzel #freedomdrive #welding #welddotcom
You donโt need magic. You need discipline, the right equipment, and settings that actually match your material and thickness.
1. Tune Pulse Settings Intelligently
For 1/8โ 6061 aluminum:
- Peak Current: 150โ200 amps
- Background Current: 30โ50% of peak
- Pulse Frequency: 100โ150 Hz
- Pulse Balance: 50โ60% background time
These numbers arenโt universal, but they give a solid baseline for heat-sensitive frame materials.
2. Use the Right Gas and Flow Rate
- Aluminum: 100% argon at 25โ40 CFH
- Steel: 75% argon / 25% COโ blend
Always double-check your nozzle and shielding. Porosity from bad gas flow often looks like a heat issue and gets misdiagnosed.
3. Re-Age Welded Aluminum
After welding, especially on 6061, consider a re-aging treatment if the frame is critical. Heating to around 320ยฐF for several hours can restore up to 90% of the lost strength.
If thatโs not feasible, reinforce the weld area or use thicker stock near the joints.
4. Follow Manufacturer Specs
Use a Welding Procedure Specification (WPS) when you can. Check the filler metal data sheet. Most of the big players like Miller, Lincoln, or Hobart publish settings for every material and wire size combo.
5. Go Synergic
If youโve got a modern welder with synergic controls, use them. These machines automatically adjust wire feed and voltage when you set your amperage and material type. Theyโre not perfect, but they take a lot of guesswork out of pulse tuning.
Welding 6061-T6 (1/8โ)
Parameter
Recommended Setting
Why It Matters
Peak Current
150โ200 amps
Balance between fusion and heat control
Background Current
30โ50% of peak
Keeps arc alive without overheating
Pulse Frequency
100โ150 Hz
Reduces peak time, minimizes HAZ growth
Pulse Balance
50โ60% background time
Helps control cumulative heat input
Shielding Gas
100% Argon @ 25โ40 CFH
Clean arc and solid bead profile
Wire Diameter
0.035โ (0.9 mm)
Smooth transfer with manageable feed rate
Where It Matters Most
- Automotive: Soft welds on a unibody car mean crash crumple zones start where you donโt want them.
- Aerospace: Even slight softening can halve fatigue life in aluminum spars and beams.
- Industrial Equipment: Frames lose rigidity, causing alignment issues or vibration problems.
Welding a frame isnโt just joining metal; itโs shaping how that structure holds up under years of use. If youโre torching your materials with the wrong pulse settings, youโre setting up a failure no one will see until itโs too late.
Final Thoughts
Frame softening doesnโt announce itself on day one. It sneaks in over time through a combination of poor settings, excess heat, and overlooked materials science.
Dial in your settings. Know your materials. Use the right gear. And when in doubt, double-check those heat-affected zones. Because once a frame goes soft, thereโs no quick fix.
Take your time, do it right, and build something that lasts. Welding is a responsibility, especially when youโre holding the frame together.